Free-air experimental manipulation of air temperature: Design principles and feasibility analysis for climate change research
This is an unfunded research idea...if this interests you Matthew is keen to chat.
Climate change will increase air temperature by 1 to 5oC over the next century. However, no climate experiments manipulate air temperature in a free-air environment i.e. with natural winds. Most climate experiments vary other temperatures (soil, leaf, canopy) or increase air temperature in enclosed spaces
Here, a free-air temperature system (ALOHA) and its design principles are proposed and tested via models and in the lab, and is shown to allow controlled heating over varying wind speeds and canopy boundary layers.
The proposed field ALOHA system showing the closed loop heating control systems to consistently increase air temperature by 1oC across varying wind speed and height. Note that the heater pipes will rapidly lose heat in the upper sections where the wind is highest, but be of lower pipe temperature near the ground, thus the pipe temperature matches the vertical wind profile and the varying need for heating with height. The prototype system would enclose a 1m diameter circle to a 1m height. Second generation systems could be square or hexagonal, with sides capable of independent heating and controlled to match the direction of the wind. Wind, air temperature and other sensors are not shown.
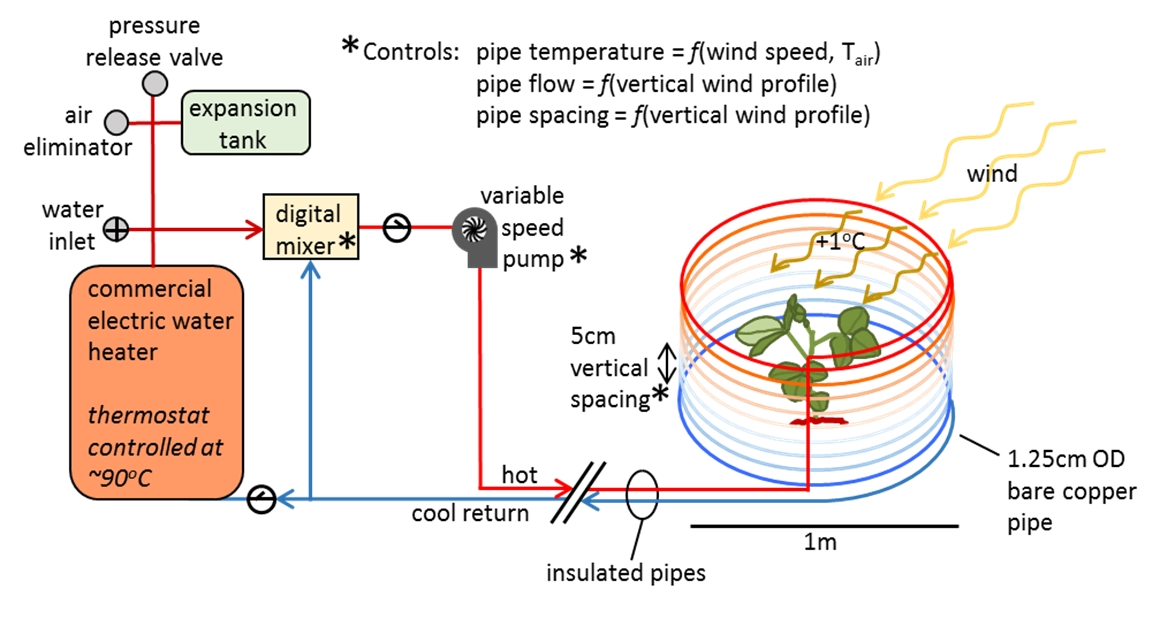
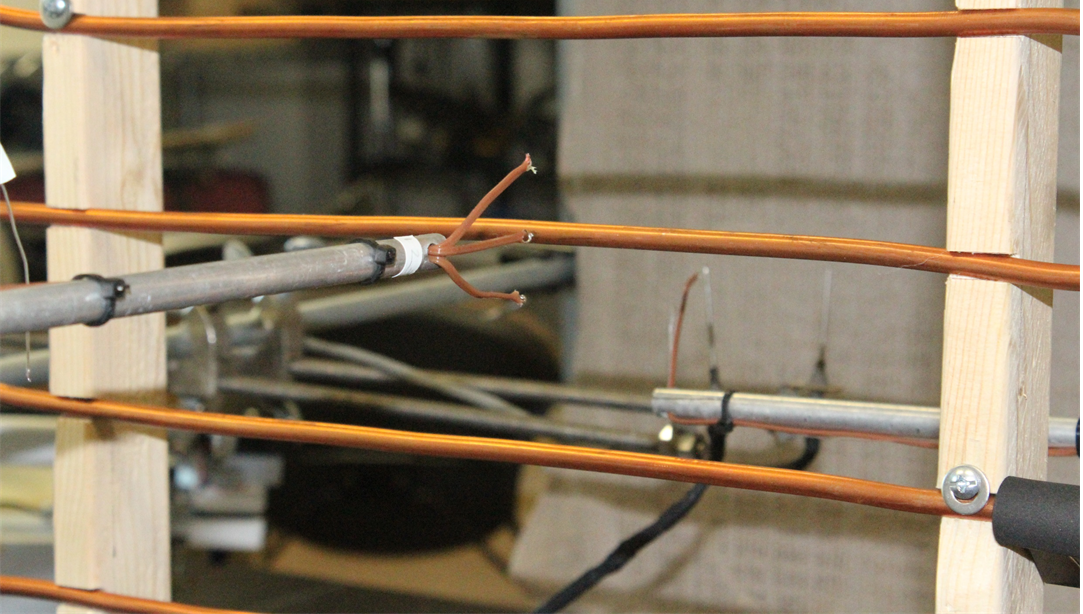
Really!? That won't work! Will it?
We built a lab system using a water bath, fan and copper tubes (see to the left). Using thermocouples at various spacings we were able to make air temperature measurements. See the next panel for the results.
Control principle 1: wind speed affects the energy needed to heat the air by a given amount, thus the pipe temperature (Tpipe) can be varied by a predictable amount relative to air temperature (Tair) to achieve constant heating. The right axis provides the calculated air temperature elevation possible for each wind speed based upon a pipe and air temperature of 90 and 20oC, respectively. Note: the lab experiment and model were created for different pipe sizes and arrangements; the model applies to the proposed field experiment. The digital mixing system with two sources of water (90oC and ambient) allows rapid control of pipe temperature i.e. in seconds.
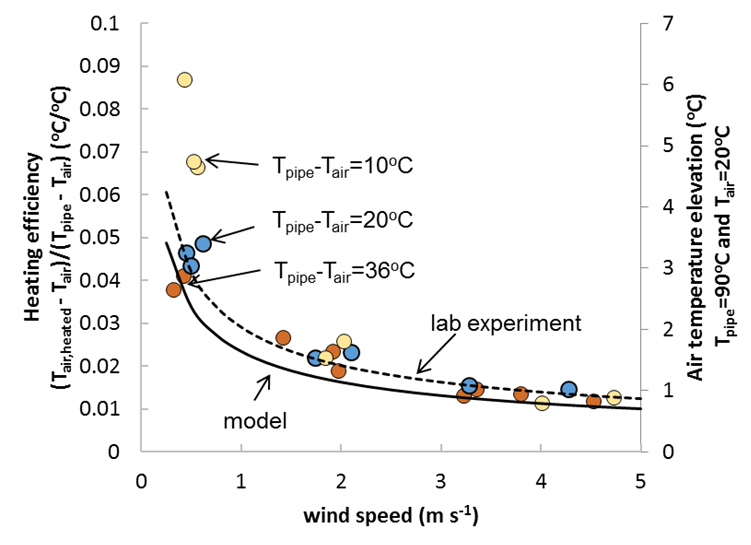
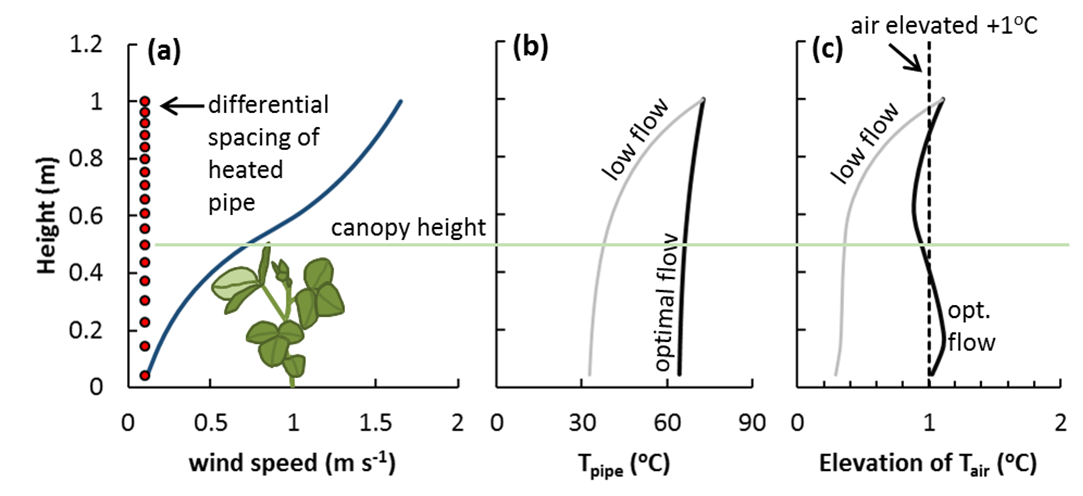
Control principle 2: wind speed varies within the atmospheric and canopy boundary layers following a logarithmic height profile (panel a), thus the ALOHA system must vary heating with height to have a uniform effect on air temperature e.g. +1oC at all heights (panel b). The digital mixer will provide a controlled input temperature into the uppermost pipe (control principle 1), a variable flow pump will then control the gradient in heat along the length of the pipe (the water enters hot at highest point and wind cools it as the water flows down). Thus, variable water flow rate could be used to provide a varying gradient of pipe temperature and consistent heating at all heights (panel b, c). Complementary to this approach is the use of a gradient of small to large gaps in pipe spacing with height (high to low), see panel a. A typical average daily wind speed for the Central Valley, CA was used for this illustration.